1 出現的問題
從2007年5月投產以來,我公司水泥預粉磨系統輥壓機故障頻繁,兩側工作壓力低且不穩定,分料閥開度的調節不合理,出輥壓機的物料粒度大,系統臺時產量低,粉磨電耗高,系統經濟效益差。
2 原因分析及處理措施
2.1 兩側壓力不穩的原因及調節
物料通過輥壓機上部入料溜子進入輥壓機的動定輥之間,由動輥側的擋料調節板來調節進入兩輥間的物料量,如圖1。經過觀察,動輥側擋料調節板伸向固定輥,造成下料點偏向于固定輥,致使固定輥側上部物料多,而活動輥側上部幾乎沒有物料,物料在兩輥之間分布不均勻,造成輥壓機的兩側壓力不穩定,結果是通過輥壓機的物料沒有被充分碾壓,出料粒度大。
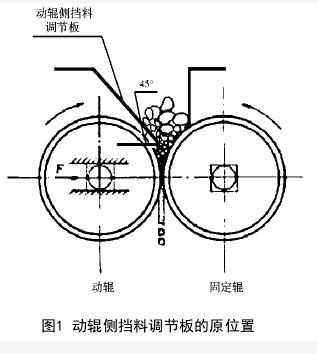
2010年8月對輥壓機活動輥側的擋料調節板進行調整,將其由原來的偏向固定輥的下料位置往動輥輥面外側移動,并將動輥側擋料調節板的角度由原來的45°調整至60°,如圖2。將輥壓機的初始輥縫調整至10 mm,使物料能夠正常下至兩輥中間,并均勻地分布,兩輥壓力波動的情況得到控制。

2.2 工作壓力低的原因及調節
對輥壓機及液壓系統進行認真地觀察和研究表明,該系統兩側初始壓力為6.0 MPa,壓力加載到5.5~6.5 MPa時設備備妥,允許開機。操作人員一般加壓到6.0 MPa再不加壓。此時由于受到初始輥縫的限制,液壓缸內的液壓油的體積是一定的,液壓缸內的油壓加載到6.0 MPa時油量偏少,即使輥縫增大,液壓缸被壓縮,油壓也達不到工作壓力8.2 MPa。
由于初始輥縫決定液壓缸的體積,初始輥縫確定為10 mm時,液壓缸體積不變,工作輥縫一般為26 mm~28 mm,變化不大。因此我們認為初始壓力的大小對工作壓力影響很大,我們將初始壓力調整為6.5 MPa,同時因穩定了入口的物料量,兩側工作壓力從7.4~7.8 MPa提升到8.2~8.6 MPa,出料粒度明顯降低。
2.3 分料閥的調節
經過輥壓機動、定輥碾壓的物料形成料餅,在兩輥間的下部出來,由于兩輥間進料充分,物料被碾壓的效果好,邊部的物料碾壓效果不及中部物料,分料閥的作用是將碾壓效果好與不好的物料進行分離(圖3)。由于一直認為分料閥開度越小越好,故一度將分料閥開度調整到20%,結果成品中一直含有10 mm左右的粗物料。打開輥壓機側門觀察,發現邊料溜子物料多且下不及,物料堆積到分料閥轉軸附近,從分料閥的轉軸下部串入成品溜子。
在摸索中調整分料閥的開度,我們發現調整到23%時,邊料溜子再沒有物料堆積現象,物料順利進入回料皮帶。
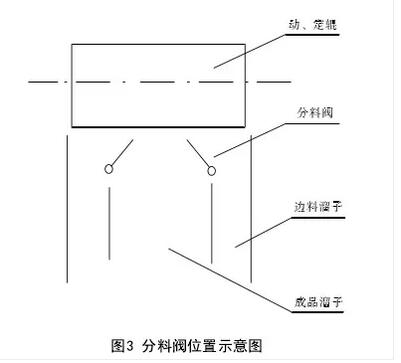
以上措施使出輥壓機的熟料平均粒徑由改造前的3.81 mm降低到1.54 mm;破碎比由改造前的4.09提高到10.10,碾壓后的物料外觀呈粉狀,入磨料層內的顆粒大多用手可以捏碎;球磨機的臺時產量提高了13.1%,系統粉磨電耗降低了16.6%。